Development Story開発ストーリー
自動車用伝動ベルト
「低フリクションロスベルト」 開発ストーリー
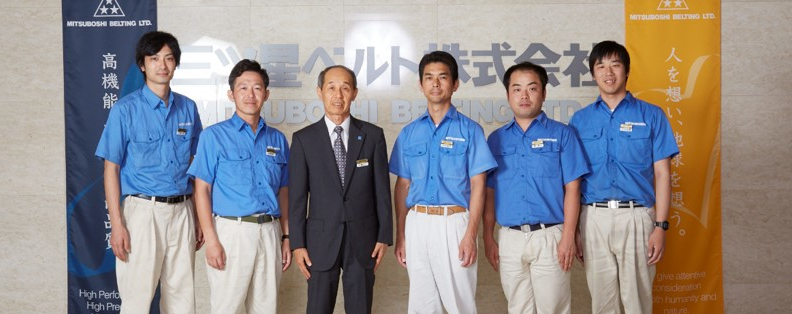
世界初の補機駆動用ベルトで低燃費と耐発音性を両立させた「低フリクションロスベルト」
低燃費化に向けた競争が激化する日本の自動車業界。そのニーズに応えるべく、三ツ星ベルトが世界に先駆けて開発に成功したのが、補機駆動システム用の低フリクションロスベルトだ。ベルトの曲がりや変形による屈曲ロスを、ベルトリブ部の内部発熱を抑えることで低減に成功。約3万点と言われる自動車部品の中から補機駆動用ベルト単体で低燃費化を実現し、さらに耐発音性や耐摩耗性といった機能も両立させた画期的な製品として、自動車メーカーへの採用が広がりつつある。
補機駆動用ベルト単体で低燃費化を実現する――。当初、お客様である自動車メーカーも、社内の技術者も不可能と考えていた低フリクションロスベルトの開発は、いかに成功したのか? 材料開発、設計、評価、営業技術ら社内各部門のスペシャリストたちによる開発チームの、約3年にわたる開発ストーリーを紹介しよう。
第1章
すべてのはじまりは、技術者のカンが引き寄せた偶然の成功からだった
誰もが予想もしない結果に、「実現できれば世界初になる」と心が躍った。
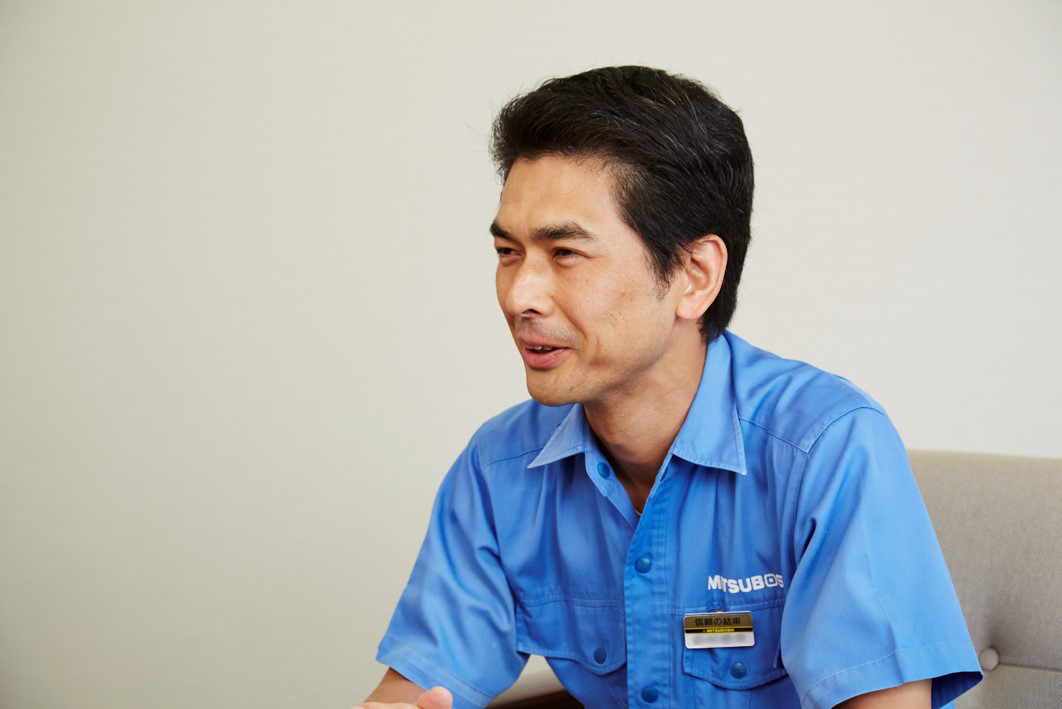
開発の発端は、自動車メーカーとの窓口である営業技術を務める田村が、取引先から受けた「補機駆動用ベルトで何か低燃費化できるアイテムはないか?」という一言だった。そこで、提案したのが、三ツ星ベルトの標準仕様である背面ゴムのリブベルト。国内メーカー向けの補機駆動用ベルトの背面は帆布が一般的だが、営業技術に移る前、長年、ベルト設計に携わった技術者としての勘から、「ゴムなら曲げやすく、ベルトの屈曲によるエネルギーロスを軽減できるのでは」と踏んでの提案だった。しかし、「正直、期待はしていなかったんです」。エンジン本体の部品ならともかく、発電機やエアコンなど周辺機器を動かすためのベルトで燃費が低減できるなど、当時の常識では考えられなかったからだ。
ところが、評価結果は予想外のものだった。約0.2%の燃費低減効果があり、メーカーの設計担当者も「ベルトでこんなに低燃費効果があるとは」と驚きを隠せない様子だったのだ。たかが、0コンマ数%。しかし、低燃費技術のアイテムも底をついてきた感があった自動車業界にあって、この数字の意味は大きかった。あいにく提案したベルトは発音性でNGが出たが、裏返せば、発音性の問題さえクリアできれば、競合他社に技術的な優位を保てる画期的な製品ができるということだ。「チャレンジする価値がある」と田村が確信した瞬間だった。
「まずはやってみよう」という社風のもと、各部署から開発メンバーが結集し、世界初への挑戦が始まった。
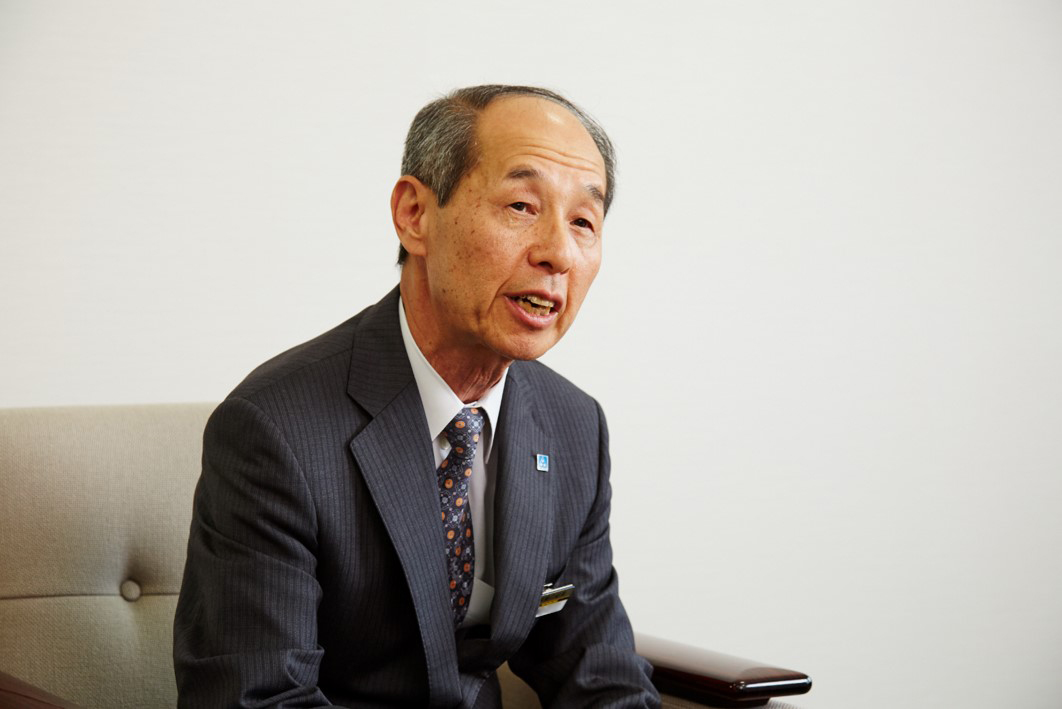
早速、ゴム配合やベルト設計、解析など技術部門の各部署に話を持ちかけ、開発メンバーを出してほしいとかけあった。田村の話を聞いた材料技術のベテラン、日根野は、「確かに今までにない発想だが、低燃費と耐発音性の向上では、ゴム配合において相反する部分があり、両立は難しいのではと思った」と振り返る。 日根野だけではなく、技術部門を統括する常務の中嶋をはじめ、誰にとっても、雲をつかむような話だった。しかし、「まずやってみよう」と前向きに考えるのが、三ツ星ベルト伝統のモノづくり魂。反対の声など出るはずもなかった。
ゴムの配合は機能開発課の日根野と部下の石黒、評価ベルトの作製や物性評価などは製品技術課の今井、フリクションロスの測定評価は実験課の繁というメンバーが選抜され、開発全体の指揮を田村がとることが決まった。石黒と今井は入社まもない新人、繁も部署に異動したばかりだったが、こうしていよいよ世界初への挑戦が幕を開けた。
第2章
ベルトメーカーとしての技術と知識のすべてを結集し、難題に挑む
ベルトの何が燃費の低減に効いているのか?開発の第一歩は、その要因を明らかにすることだった。
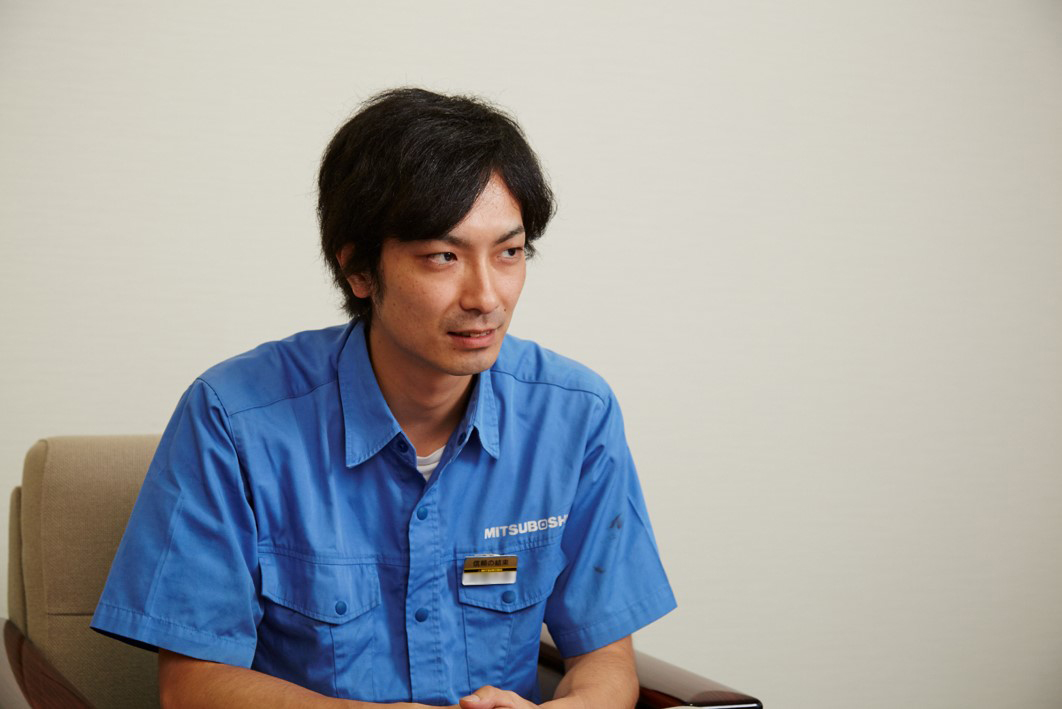
まずしなければならないことは、ベルトを構成する背面、リブ、心線の三つの部材のどこに屈曲ロスの低減に効いている要因があるかを洗い出し、理論づけることだった。その低減理論の検証にあたったのが、入社2年目の石黒。「長くゴムの配合設計に携わってきた人間には、固定概念がある。全く新しい技術に挑戦するには、まっさらな発想が必要だ」と、先輩の日根野が抜擢した。石黒は、思いのほか早くやってきた新製品開発のチャンスに喜びと不安を感じつつ、「失敗してもいいから、好きなようにやってくれ」という言葉に押され、自分なりの推論を加え、ゴム材料とベルトのデータ解析にとりかかった。
一方で急がれたのが、ベルトのフリクションロスを測定する方法の確立だった。試験機や製造設備の開発・製造ができる技術部隊が別用途で開発した試験機を応用し、測定方法の確立を託されたのが、実験課の繁だ。初めての経験だったが、毎日のように試験機のトルク計と向き合い、測定結果がばらつくという課題を1カ月ほどかけて解決。0.1Nmの精度までフリクションロスの測定が可能になった。これによってベルトの構成部材ごとのロス測定が一気に進み、結果、リブゴムの配合がロス低減に大きく効いていることが明らかになった。開発のスタートから半年後のことだった。
相反する燃費向上と耐発音性をどう両立するのか。最適なゴム配合を模索する日々の中で、ついに光が見えた。
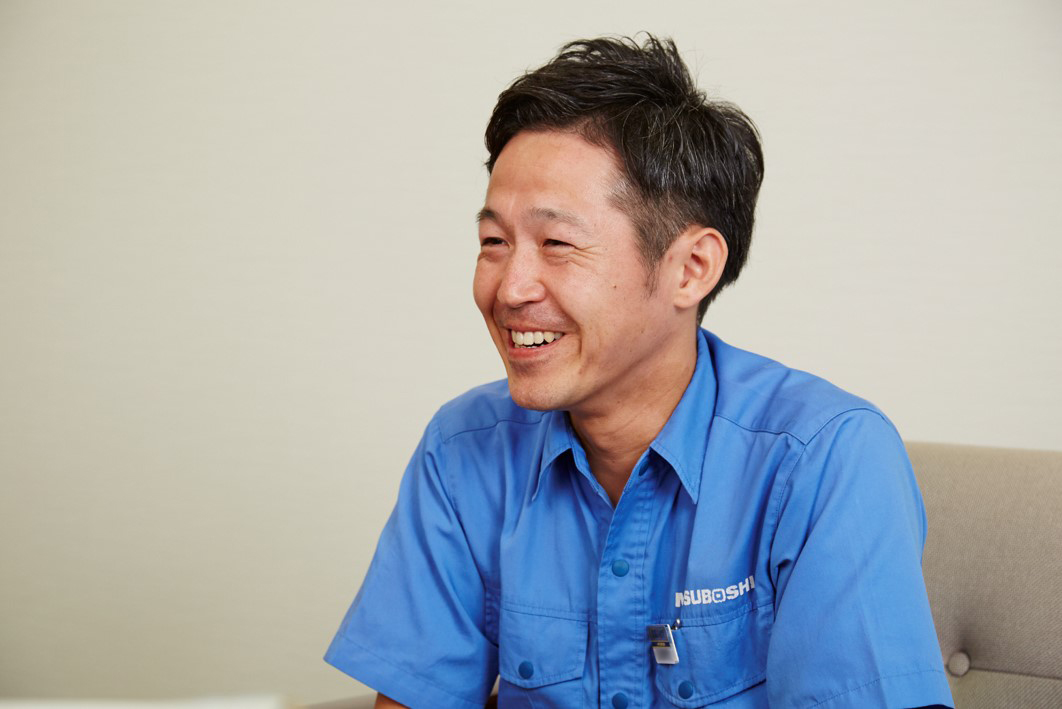
開発ミーティングでは当初、「効いているのはゴム配合ではなく、形状ではないか」など多様な意見が出ていた。しかし、要因がリブゴムの配合にあると絞り込まれてからは、発音性の解決へと開発のベクトルが定まっていった。しかし、その音こそが最大の難所だった。
長年の研究で、ベルトの内部発熱を低減する手法は確立しつつあったが、その手法を用いると耐発音性だけでなく耐摩耗性、生産性までもが悪化してしまうのだ。耐摩耗性や生産性も確保しながら、いかに顧客が求める耐発音性を実現させるのか?
主に石黒が膨大な社内の材料データベースを参考に、配合開発のトライ&エラーを繰り返し、加工面では混練条件や圧延条件などを検討。実用化の成否を日根野が見極め、今井が工場の製造部門と協力し評価用ベルトを作製しては、繁が実車で発音試験を繰り返した。これが、ほぼ週一のハイペースで続いた。メンバー全員が他の案件も抱えながら多忙を極めたが、顧客に開発の進捗状況を報告に行った田村が戻ってくると、技術部門の一角にすぐに集まって、次の手をどう打つか若手もベテランも関係なく意見を出し合った。
リーダーの田村は、「新技術・新製品を開発するのがメーカーの義務」という西河会長が日頃から話していることを念頭に、「世界初のベルトを必ず開発する」という信念を持ち、「もう一歩だ」とメンバーに発破をかけ続けた。しかし、発音試験で良い結果が得られないこう着状態の中、「暗礁に乗り上げるかもしれない」と思った時期があったという。そんなときだった。世界中から三ツ星ベルトグループの各部門の責任者が集まる部門長連絡会で耳にした、「新しいことに挑戦しようとする人は、結果に関係なく評価する」という垣内社長の言葉に再び力をもらい、自らを奮起させた。
そして、ついに「これなら発音が抑えられる」と、日根野が太鼓判を押す最適な配合が見つかり、開発は最終段階へと進むことになった。
第3章
拓かれた補機駆動用ベルトの新たな可能性
ギリギリのラストチャンスで勝ち取った、発音試験「合格」の判定。
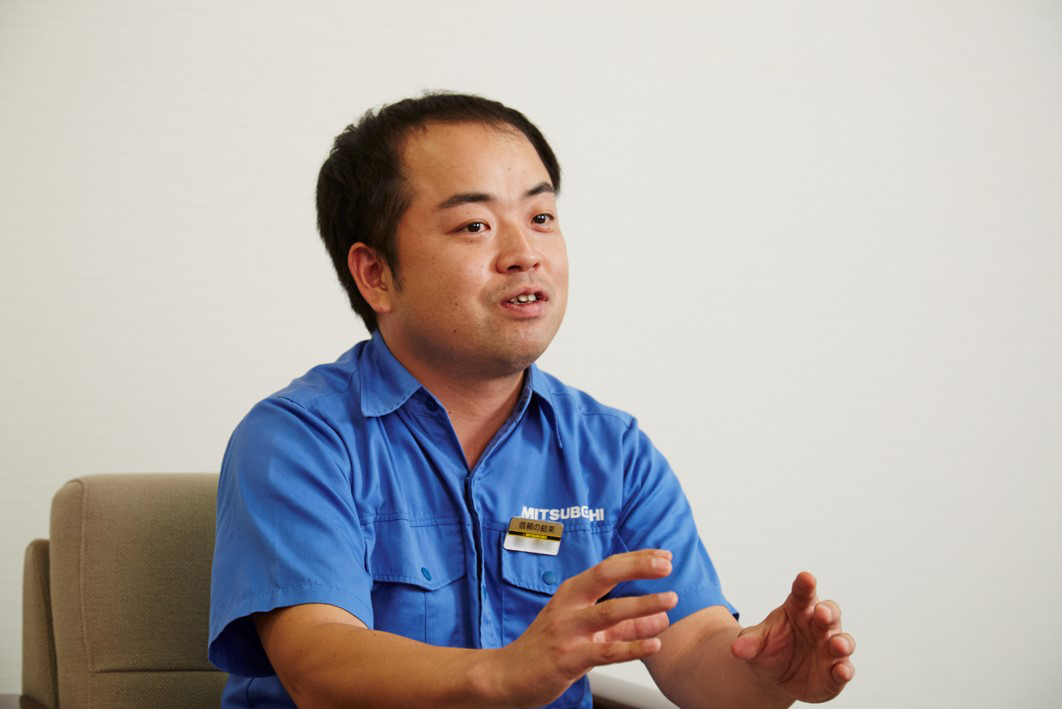
絞り込まれたゴム配合による試作ベルトは、社内の実車試験でも良い結果が出た。耳で聞いてわかるほど、発音が抑えられていたのだ。すぐに顧客が開発中の車両でテストしたかったが、量産が近づき他の評価を行うので車両が確保できないという。そこで、田村と繁の提案でレンタカーを持ち込み、客先のエンジン振動および異音評価担当者とともに発音試験を実施することになった。このタイミングで発音試験をクリアできなければ、顧客の新車の立ち上げに間に合わない、ラストチャンスだった。
あえて厳しいCVT(無段階変速機)を搭載した車両で試験をしてきた。顧客の評価基準を満たす発音レベルをクリアしていることも確認済みだった。だが、本番では何があるかわからない。緊張しながら、発音試験の評価を待つ2人に、もたらされた結果は「OK」。担当者の「このベルトは当たりですね」という言葉に感動がこみ上げてきた。結果はすぐに、社内で待つ他のメンバーに電話で伝えられた。「うれしさと同時に、安堵がこみ上げてきた」というのが、日根野たちメンバーの正直な気持ちだった。
いよいよ量産化・発売へ。そして、次世代の低フリクションロスベルトの開発へ。
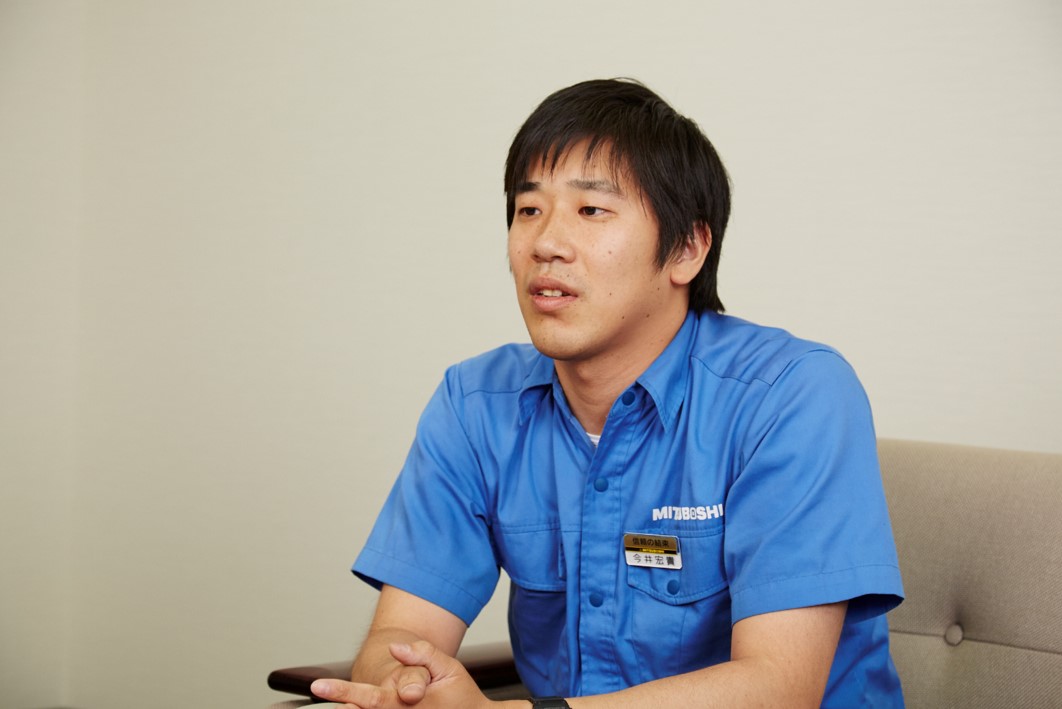
量産ラインの立ち上げにあたっては、石黒の同期、今井が奮闘した。「最も苦労したのは、製品仕様や使用材料、効果や製造方法、コストなど膨大な開発の評価結果をまとめ、生産も営業も集まる評価会議で量産のゴーサインをもらうことだった」と振り返る。直属の上司や開発リーダーの田村をはじめメンバーの助けも得て、量産の決定が下り、その後、生産準備が急ピッチで進められた。量産化に向けて解決するべき課題はまだあったが、その頃には、テレビや雑誌、自動車メーカーのHPなどで、自分たちが開発した低フリクションロスベルトを搭載した新車が発表され始め、「苦労が報われる思いだった」という。
そして、いよいよ開発のスタートから3年を経て、低燃費性を前面に打ち出した顧客メーカーの軽自動車が発売された。顧客からは燃費アイテムとして燃費効果試算にも含めていると高く評価され、その年の「低燃費技術賞」の受賞へとつながった。
低燃費と耐発音性を両立させた世界でも初めての補機駆動用ベルト――三ツ星ベルトの「低フリクションロスベルト」に相当する製品は、いまだ競合他社も開発できていない。そればかりか、その後、三ツ星ベルトでは、耐発音性は維持したまま、さらに低燃費を実現する次世代製品の開発にも成功し、採用メーカーは国内自動車メーカー各社へと広がっている。
トルクロス測定条件にて走行後のサーモグラフィー
低フリクションロス仕様の発熱性が低い(=屈曲発熱小さい)ことが確認できます。
低フリクションロスベルト
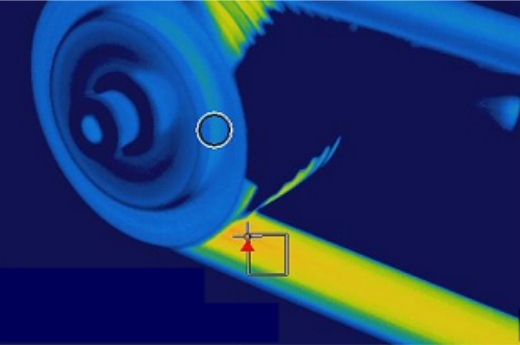
標準ベルト
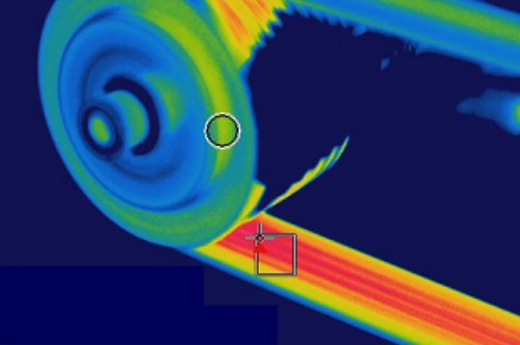
さらなる低燃費への要求に、技術を進化させ、応えていく。
当初、誰もが考えもしなかった未知の技術に、メンバーが一丸となって挑み続けたことで、拓かれた補機駆動用ベルトの新たな可能性。その成功体験は、開発に関わったメンバーの自信につながっただけではない。ベルトメーカーとして将来的に社会に貢献するために何ができるか、そのことを常に考え、仲間と議論することで技術を進化させてきた三ツ星ベルトの風土に、「新技術は我々が生みだす」という強い意識を植え付けたことは間違いない。ますます厳しくなる低燃費への要求に応え、さらに、世界中の内燃自動車に低フリクションロスベルトを広めるために、これからも三ツ星ベルトの挑戦は終わらない。
人物紹介
我々がやらねば、誰がやる!ベルトメーカーの誇りをかけて挑んだ、世界初のベルト開発
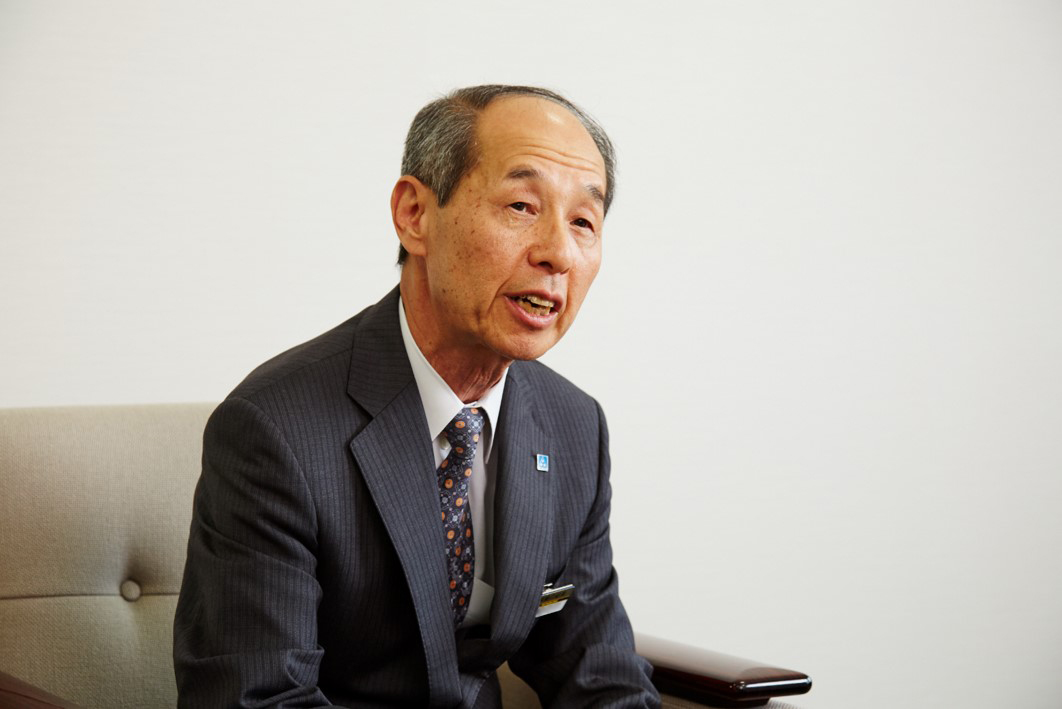
中嶋 正仁
取締役 常務執行役員
産業資材事業部門 技術統括担当
低燃費と耐発音性を両立させた低フリクションロスベルトの開発成功は、国内市場が縮小する中で我々がシェアを伸ばし、さらに世界に向けて新しい技術を発信できた点で、大きな意義があります。いつも社内の技術者には、開発では「ヘッドワーク」(頭を使って、全体を見渡す)、「ハートワーク」(執念を持ってやりぬく)、「チームワーク」(技術各部署が一つの課題にベクトルをあわせる)の3つが必要だと話しています。これら三ツ星ベルトのモノづくりへの姿勢がうまくかみ合ったことが、開発成功の要因だと考えています。
今後、エンジンの小型化が進めば、ベルトの音の影響が大きくなるため、耐発音性の向上は付加価値になるとみています。今回のように若手にも早くから役割を担ってもらうことで、技術やモノづくりへの姿勢を伝承し、低フリクションロスベルトを、さらにその先の技術へと進化させていきます。
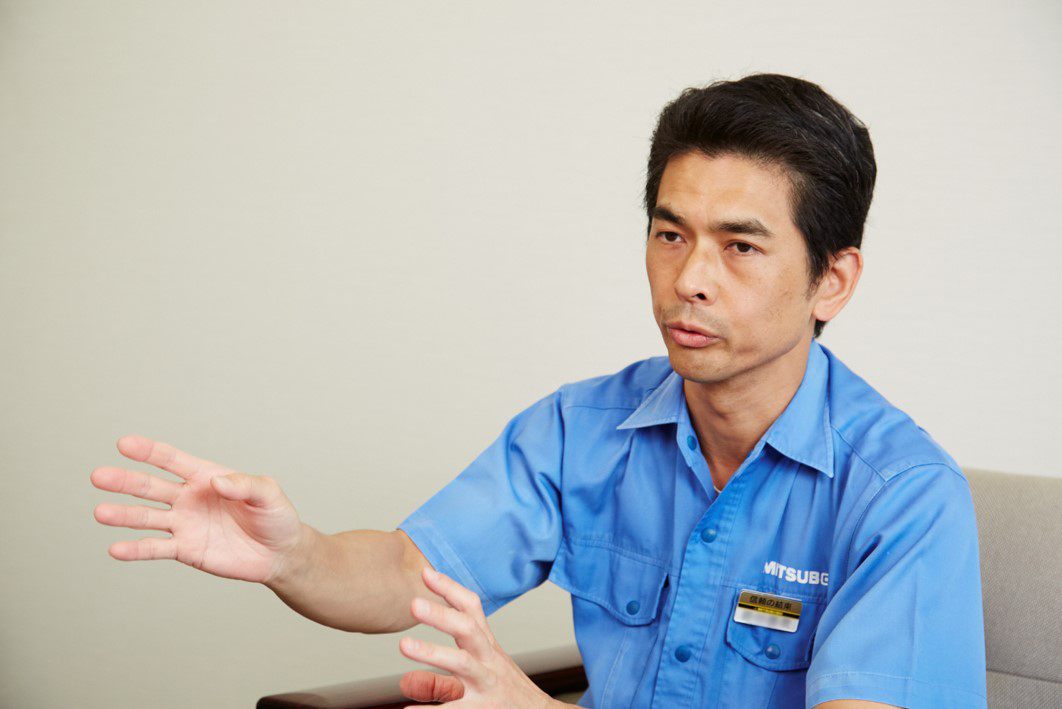
田村 昌史
産業資材技術統括部
製品技術第1部 営業技術課
世界初のベルトを開発でき、補機駆動用ベルトに新たな分野が確立できたことに、達成感を感じています。高機能・高精密・高品質な製品の提供を基本方針に、設計・ゴム配合・試験評価・解析、営業技術など、開発を行ううえで問題点があっても迅速に解決案が導けるさまざまなエキスパートが在籍し、必要ならば試験機や製造設備まで開発できる体制が三ツ星ベルトの強み。今回も、各分野のスペシャリストが集まり、多くの方の協力やアドバイスを得られたことで、開発を無事完了することができました。自分の掴んだ情報から開発が始まり、企画・開発・お客様の承認・生産と最後まで関わったことで、多くの経験を得て、成長することができました。
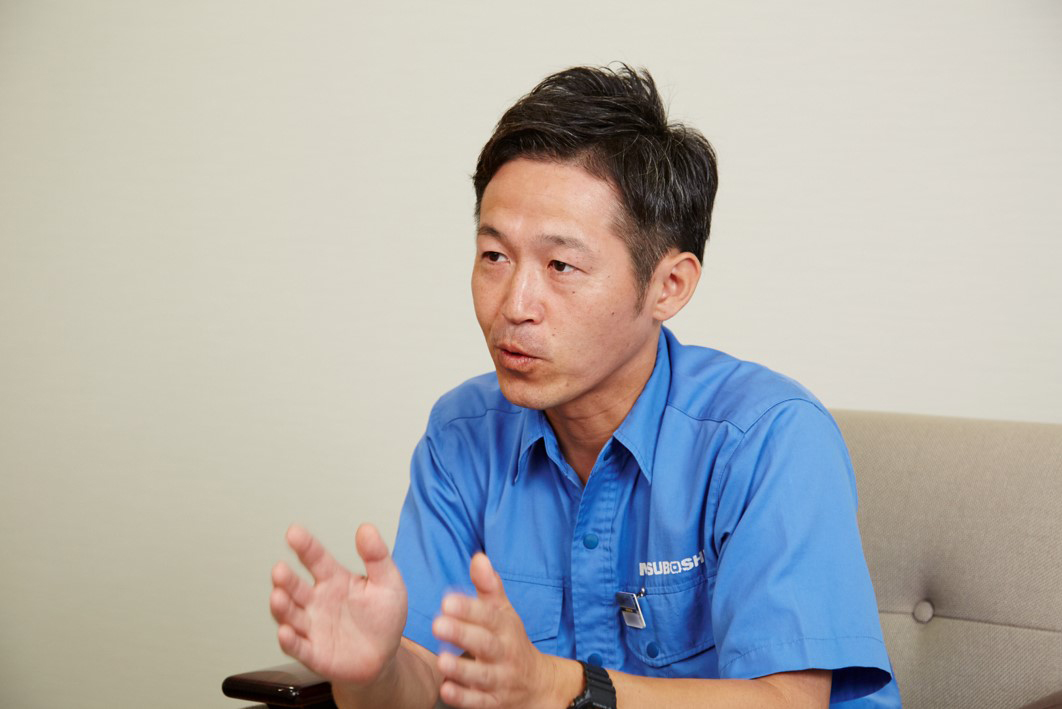
日根野 順文
産業資材技術統括部
材料技術部 機能開発第2課
問題があればすぐに集まって、社歴や部署を超えて意見をぶつけあえる社風があるから、実行や決断のスピードも速い。それが開発を成功に導いた三ツ星ベルトの強みのひとつだと思います。個人的には、開発のストーリー(工程)全体を意識しながら、ターニングポイントで的確な判断をすること、バックアップの準備をしておくことを心がけました。開発が進み、お客様から良い回答が得られるにつれ、チームの一体感が増し、皆で達成感を共有できたことは、技術者冥利につきます。
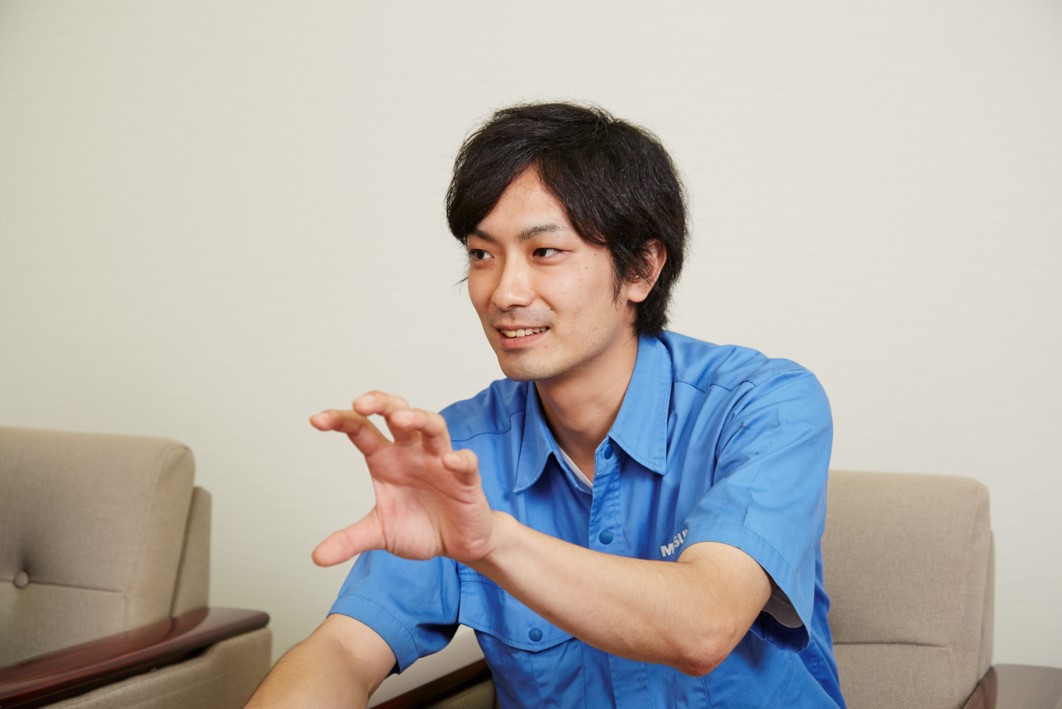
石黒 久登
産業資材技術統括部
材料技術部 機能開発第2課
「固定概念を持たず、自由にやってもらっていい」と言われたものの、固定概念が何かもわからない状態からのスタート。不安はありましたが、「やらずに後悔するより、やって後悔する方がよい」と、思いつくことは全てやる気持ちで臨みました。ゴムは知れば知るほど、未知の部分が大きい材料であるため、たくさんの理論を踏まえながら、先入観を持たず、実際の経験に基づく理論を自ら確立することが重要と身を持って感じることができました。また、膨大なデータ解析を通じて、ゴム材料とベルト物性の相関性を確認できたことは、技術者として大きな経験です。今後は、ゴムに限らずベルトに使われる材料全般に精通し、誰にもマネのできないモノを開発してみたいと思っています。
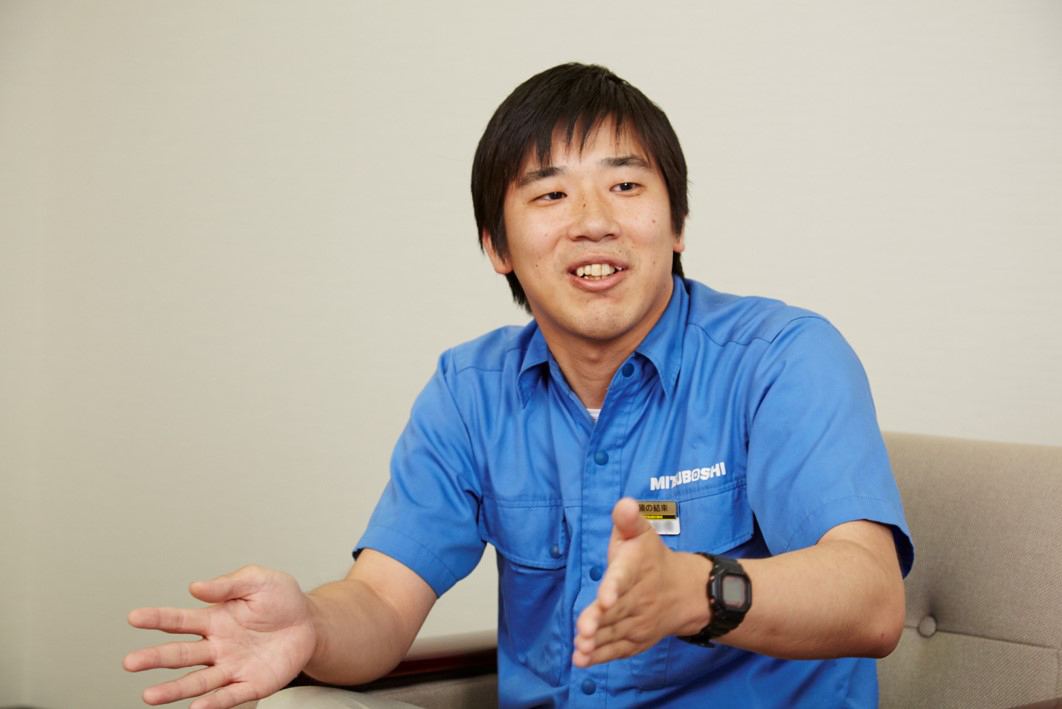
今井 宏貴
産業資材技術統括部
製品技術第2部 先行開発課
製品開発の経験が浅く、一人では右も左もわからない状態でしたが、経験豊富な先輩にフォローしてもらい、自分の職務をまっとうすることができました。工場で日々生産ラインが動く中、試作ベルトの製作のためにラインや人手を割いてもらう交渉を行うのも私の仕事でした。いかに納得を得られる伝え方をするかなど、開発チーム内はもちろん、生産や営業など他部門とのコミュニケーションが不可欠な業務でしたので、技術者としてだけでなく、人間的にも大きく成長できました。現在は、新規開発の部署で製品設計をしています。材料の知識も学び、いずれは「こういう特性を持っている製品をつくりたい」という提案型のモノづくりができるようになりたいですね。
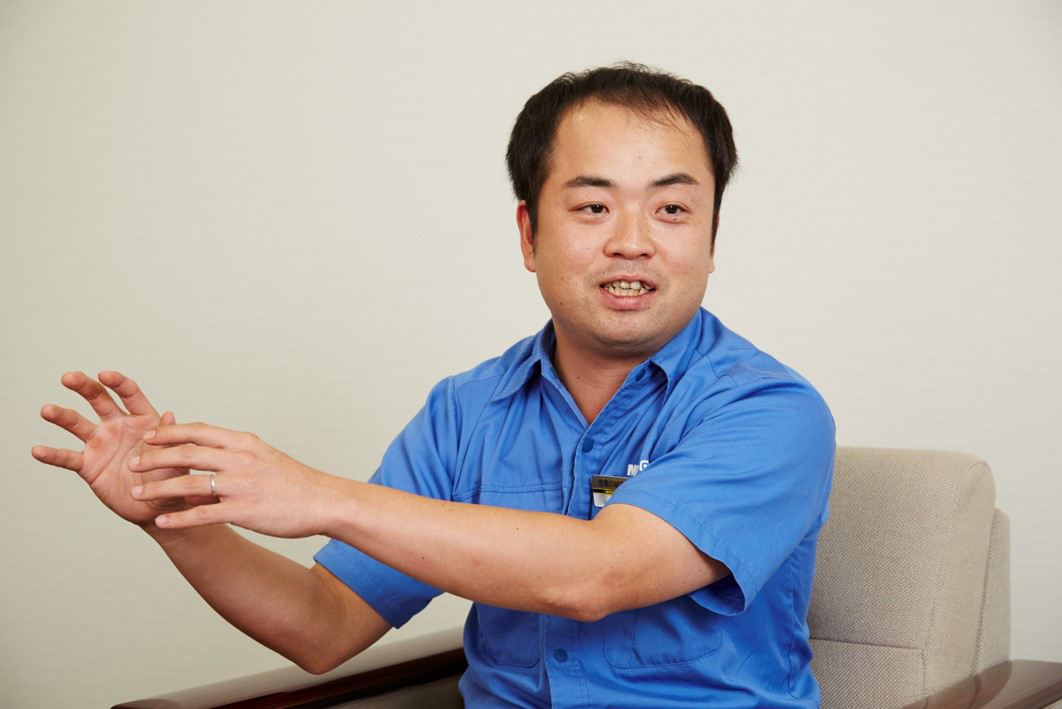
繁 貴之
産業資材技術統括部
製品技術第2部 設計第1課
試験評価の経験はほとんどないまま、開発メンバーに抜擢されましたが、フリクションロスに関する試験は「任されている」という責任感を持ち、正しい試験結果を出すことに心血を注ぎました。お客様の基準ロスの目標をあと少しでクリアできるところまできたときは、だからこそ、万が一にも試験の結果を甘く見積もることがあってはならない、世に出てから大きな迷惑をかけることになると肝に銘じていました。定期的な打合せでは、課題を抽出し、各自がどう対処するのか具体的に検討し、役割を明確にしていたので、常に緊張感を持って取り組めたのが良かったです。現在、製品設計を担当するお客様から低フリクションロスベルトについて問合せを受けたときは、自信を持って提案できるのが、うれしいですね。
※登場する社員の所属部署や社歴は、開発当時のものです。